Wie ist der Elroq entstanden? Nicht auf die übliche Weise!
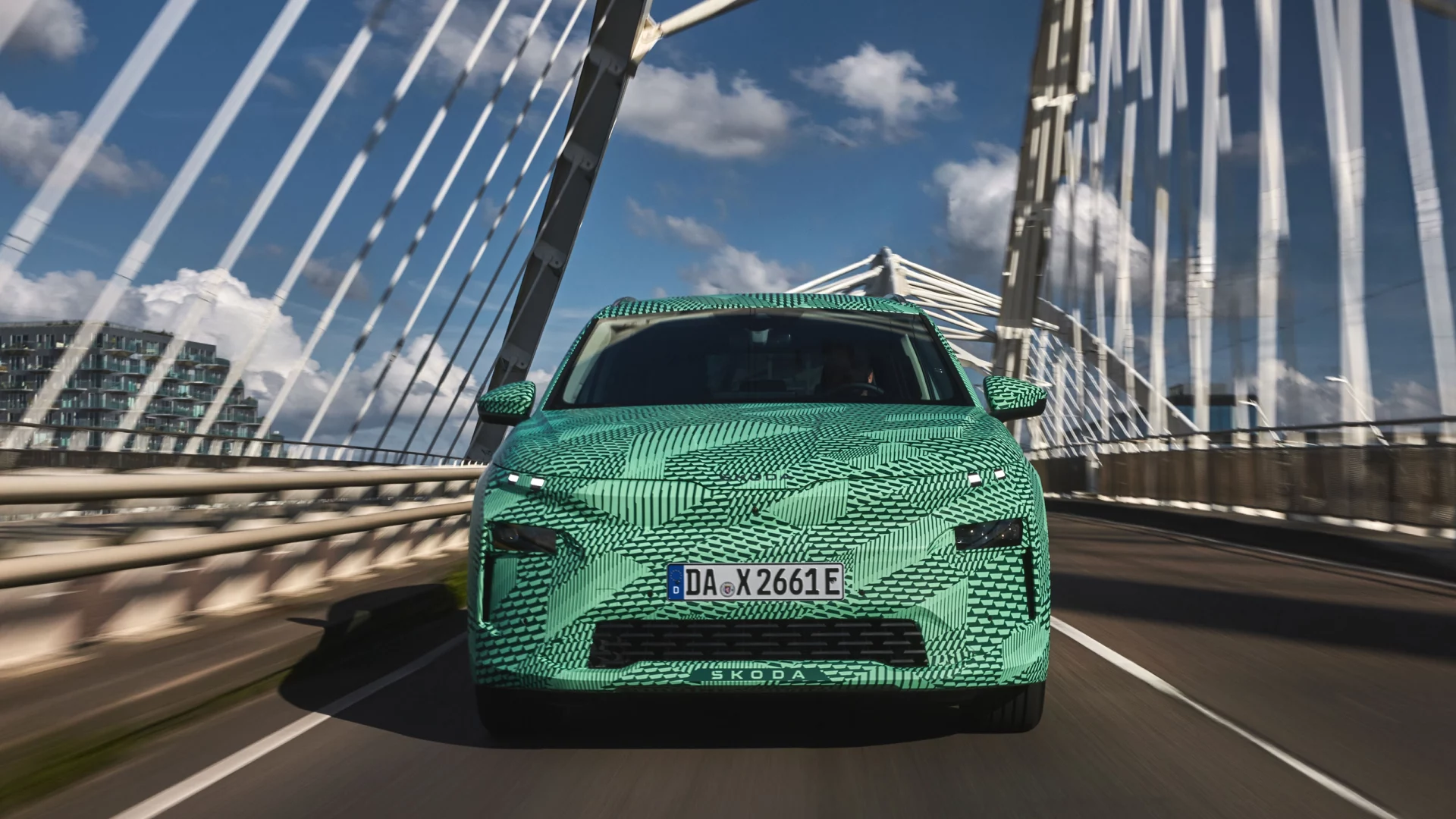
Bei der Entwicklung des elektrischen Elroq haben die Expertinnen und Experten von Škoda eine gänzlich neue Methode ausprobiert. Die Vorbereitung der Testwagen für die Vorserienerprobung verlief anders als üblich, denn die Autos wurden direkt vom Band zum Testen geschickt.
13. 9. 2024 eMobilitätUm die Anzahl der teuren Prototypen zu minimieren, die ein Autohersteller produzieren muss, setzt die Entwicklung zunehmend auf eine Reihe virtueller Methoden. „Die ersten Testwagen wurden in Zusammenarbeit mit anderen Abteilungen direkt am Fließband gebaut“ sagt Milan Vostrý, Projektleiter für die Vorbereitung der Prototypen.
In mancher Hinsicht erschwert die Tarnung die Akustikprüfung, aber das ist nichts, womit die Škoda Experten nicht umgehen könnten.
Die Prototypen, von denen meist mehrere Dutzend hergestellt werden, kommen im Normalfall aus einer darauf spezialisierten Werkstatt. „Auch wenn wir die finale Lackierung in unserer Werkstatt vorgenommen haben, durchlief das erste Elroq-Modell oder Teile davon eine Schweißerei, eine Lackiererei und eine Montagestraße“, betont Vostrý.
„Ermöglicht wurde das durch die hervorragende Zusammenarbeit vieler Abteilungen – von unserer Prototypenwerkstatt über die Konstruktionsabteilung, die Lackiererei, die Schweißerei, die Montage, die Produktionsplanung, die Montagetechnik und die Logistik bis hin zum Werkschutz“, so der Projektleiter. Durch diese Teamarbeit entstanden in zwei Wellen insgesamt 16 Testwagen, die von den Fachabteilungen für die Erprobung genutzt wurden. „Es handelte sich dabei nicht um Prototypen im eigentlichen Sinne“, erklärt er und fügt hinzu, dass die Fahrzeuge bereits viel näher an den Serienfahrzeugen waren, als dies bei Prototypen normalerweise der Fall ist. „Unser Verfahren erleichterte auch die nächsten Schritte der Produktionsvorbereitung und Montage in der Halle M13 – einschließlich des Produktionsbeginns der Vorserienfahrzeuge.“
Die Elroq Prototypen wurden auf der Linie M13 gefertigt, auf der auch der Elektro-SUV Enyaq (im Bild) und der Octavia montiert werden.
Der Sound im Fokus
Ein großer Vorteil der Methode: Zahlreiche Abteilungen konnten ausprobieren, wie sich das Auto verhalten wird. Die produzierten Fahrzeuge gingen hierfür direkt in die eigentliche Erprobung, indem sie beispielsweise Haltbarkeitstests oder die vorgeschriebenen Crashtests durchliefen.
Auf diese Weise konnte Škoda oft Features an den Autos testen, die dem Serienmodell sehr ähnlich sind und die normalerweise an sogenannten „Mules“ erprobt werden – das heißt an Fahrzeugen, die die Technik des neuen Modells enthalten, aber anders aussehen. Sie sind für manche Tests geeignet, für andere aber überhaupt nicht. „Jegliche Art von Tarnung erschwert unsere Arbeit“, sagt Michal Němec, Koordinator für Akustiktests. Seine Abteilung testet alle Geräusche, die ein Auto macht – einschließlich der aerodynamischen Geräusche. Sie können durch jegliche Abweichung vom endgültigen Design verändert werden.
Škoda Elroq
Sein Team muss die Autos unter absoluter Geheimhaltung testen. Ziel ist es, eventuelle Mängel festzustellen, damit sie so schnell wie möglich behoben werden können. „Wir testen in unseren Labors, auf dem Škoda Polygon, aber auch in einem aeroakustischen Tunnel in Italien und auf einer Strecke in Wolfsburg“, sagt Němec. „Wir erproben alle Fahrmodi, mit denen die Kundin oder der Kunde konfrontiert werden könnte, und zwar unter verschiedenen klimatischen Bedingungen und auf unterschiedlichen Untergründen“, fügt der Ingenieur hinzu. Was dabei nicht einfacher im Vergleich zu einem Verbrenner sei: ein Elektroauto auf Geräusche zu testen.
Während die Geräusche des Verbrennungsmotors – also der Ansaug- und Auspuffanlage – bei einem E-Modell nicht berücksichtigt werden müssen und die Einhaltung der gesetzlichen Geräuschgrenzwerte kein Problem darstellt, muss man sich hingegen umso mehr auf andere Bereiche konzentrieren. „Ohne ein konventionelles Triebwerk treten andere Geräusche in den Vordergrund, die bei Fahrzeugen mit Verbrennungsmotor verborgen bleiben können“, erklärt Němec. Das bedeutet, dass sich die Ingenieurinnen und Ingenieure beispielsweise stärker auf aerodynamische und Reifengeräusche konzentrieren müssen. Hinzu kommen verschiedene andere Geräusche, die durch Unterschiede in der Produktion der Autos beeinflusst werden. Diese werden sowohl objektiv anhand von Tonaufnahmen als auch subjektiv, also durch Testfahrerinnen und -fahrer oder andere Personen, bewertet.
Elektroautos können neue Geräusche erzeugen – etwa hohe oder tiefe Töne, die durch die Hochspannungselektrik verursacht werden. Eine Besonderheit ist das obligatorische Geräusch, das sie bei Geschwindigkeiten zwischen sechs und zwanzig Kilometern pro Stunde abgeben müssen. „Wir müssen diese Warnung für Fußgängerinnen und Fußgänger vor einem herannahenden Elektroauto genau abstimmen, um alle gesetzlichen Anforderungen zu erfüllen“, betont Němec.
Die Tests, denen die Autos unterzogen werden, sind überaus gründlich und anspruchsvoll. Allein die Tests im Bereich Akustik dauern für den Elroq mehr als 2.000 Stunden – das sind mehr als 250 Acht-Stunden-Tage. In der Realität gehen die Tests natürlich schneller vonstatten, weil mehrere Autos gleichzeitig an die Reihe kommen und die Arbeit im Schichtbetrieb erfolgt. Die Akustiktests machen jedoch nur einen Bruchteil während der Fahrzeugentwicklung aus. Neben den bereits erwähnten Crashtests wird beispielsweise auch die Software des Fahrzeugs überprüft und es werden Klimatests – unter anderem in speziellen Klimakammern –, verschiedene Qualitäts- und Verifizierungskontrollen sowie Homologationstests durchgeführt. „Es gibt viel zu tun, denn das Ziel ist, dass das Auto, das an die Kundin oder den Kunden ausgeliefert wird, von höchstmöglicher Qualität ist“, fasst Michal Němec zusammen.