Here is where future Škoda cars are born. Look inside the secret model workshop.
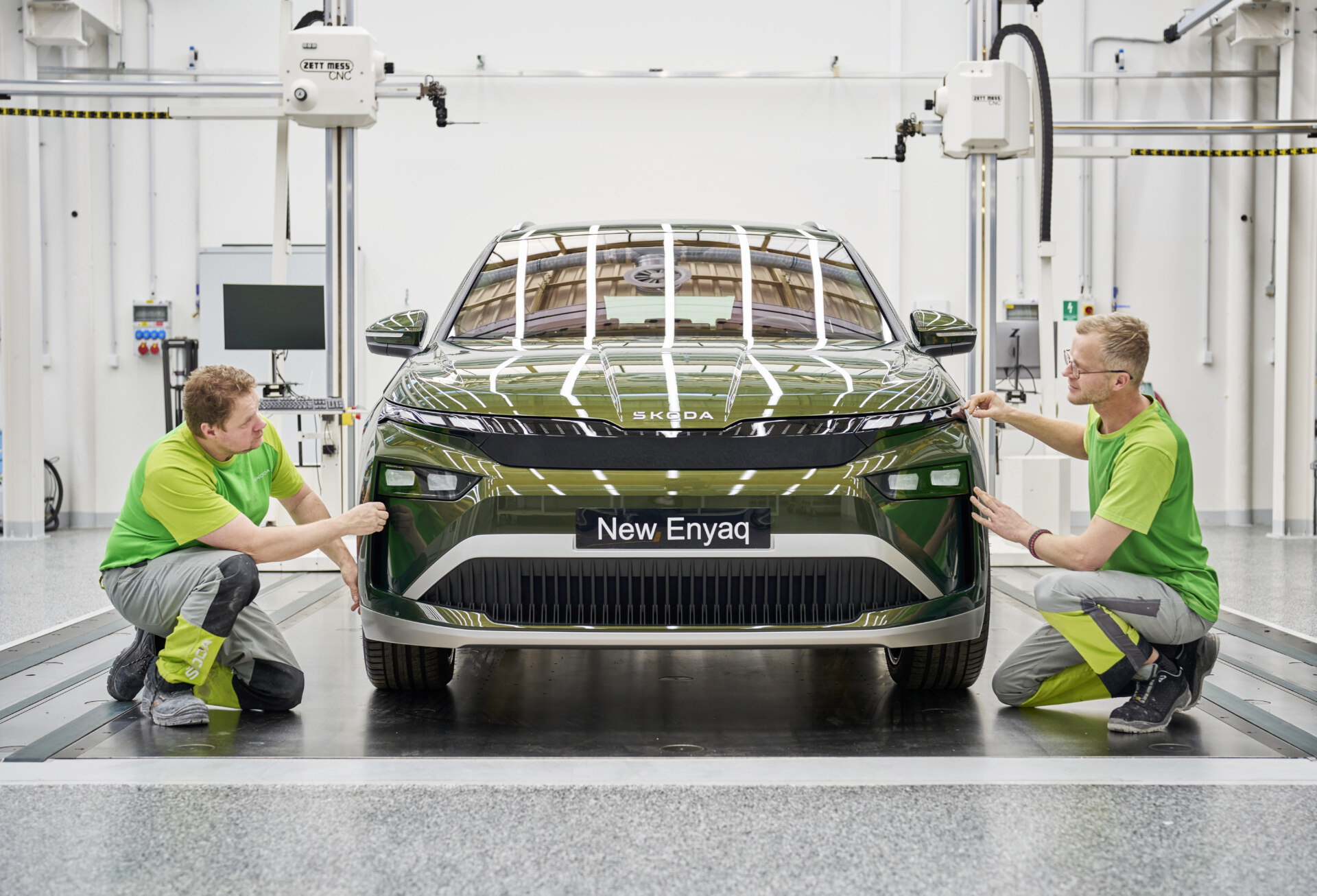
Every new car begins as a concept, or an idea created by designers and engineers. At a certain point, however, ideas and digital data start to take physical form as models. Find out how they are made.
11. 2. 2025 eMobilityThe specialized model workshop at Škoda Auto’s Technical Development is one of the most tightly guarded areas. It is here that future cars take their first physical shape, long before they are unveiled to the public.
The latest creation to pass through the model workshop that the public already knows is the new Škoda Enyaq. In this case, the model workshop cooperated with several other departments of the automaker, which make use of its services. Many different models are created here, for various needs and purposes.
The basis for the clay model is a structure in a combination of steel, plywood and polyurethane foam
The most well-known models for the public are probably the clay models, which are made in the design department. The model workshop at Škoda Auto’s Technical Development is also involved in their preparation. It constructs the base model onto which designers apply the clay and "sculpt" the desired shapes of the future car. Every model starts with a mix of steel profiles and tubes, plywood, and polyurethane boards that define the basic proportions.
These materials (and much more) are stored in an impressive warehouse. The space is narrow but 16 meters high. Between the racks, which reach up to the height of a four-story building, there is only room for one special manipulator. The person operating it must not suffer from vertigo, as they are lifted to great heights while retrieving materials.
Model of the new Škoda Enyaq in the Škoda Auto Technical Development model room
"Every model construction is preceded by our digital design preparation," points out Jaromír Pavlíček, the model production coordinator who is guiding us through the workshop. Designers often must figure out how to construct the model and how to "assemble" it. The design of the construction also depends on the purpose of the model.
A wide scope
In addition to the foundations for clay models, so-called hard models are also created here. These models are made of relatively solid material and are not expected to undergo significant shape changes during the production and completion of the model. One of the first models created during the car development process is the ergonomic interior model, on which developers test the accessibility of controls and the overall interior space.
In cooperation with the design department, so-called proportion models are also made. These models are carved from polyurethane foam and are used to assess the shapes of the car being developed. They typically have a matte finish. "We work very quickly on them; from the moment we receive the final data to the completion of the model, it often takes only several working days," mentions Pavlíček. To work efficiently with large car models, there are six milling stations: three large ones for machining the entire 1:1 scale models and three smaller ones for producing individual components.
Accuracy is extremely important for models, which is why they have their own measurement center in the model room of Technical Development
Another task that the workshop has to master is the creation of interior models to assess colours and materials. "To achieve the appropriate decor, we coat parts with a special foil, and we also paint the parts and the entire models ourselves," explains Pavlíček. The model workshop even has its own paint shop. The pinnacle of design work is special models for the final design assessment. These models can even be moveable, are fully painted, and their headlights and other components illuminate exactly as they should in the final car.
"We can produce practically all of their components ourselves," adds Pavlíček. For example, the individual parts of the headlights are mainly created using 3D printing. The process starts with a clear version, and the colour of the headlights is added with a tinted coat of paint. The shapes, fit, and optical properties are manually adjusted, with the polishing of one part sometimes taking an entire shift. It’s very precise work.
In the model shop, they can try different variants of visual parts on the upcoming cars
But the scope of the model workshop doesn’t stop there. It has its own metalworking operation capable of machining even engine blocks. This is where individual metal parts for entire models are made, as well as prototype parts for real-world prototype testing. Some parts are even made here for Škoda Motorsport.
The model workshop also prepares models for testing in the aerodynamic tunnel. Based on the requirements from the development department, several variants of parts affecting aerodynamics are created. The designers then must figure out how to ensure that these parts can be easily and quickly replaced while still withstanding the high airspeeds in the tunnel. "The reason is that work in the tunnel must be as time efficient as possible," explains Pavlíček.
With the models, everything has to fit, an important part of working with them is checking the dimensions or perhaps matching the joints
When it comes to complete models, the most complicated task involves two types of control models. The first one is the FKM (model for surface control) model used for process-oriented fast surface design, the second one is the so-called DKM (model for control of CAD data) data control model, which is already the final model that meets significantly stricter criteria in terms of accuracy than the series cars. Every gap, every part, must fit precisely within tolerances of a fraction of a millimetre. These models are fine-tuned in loops with several other departments, from technical development to design, production, and quality. The result is final data used to manufacture production car parts and entire vehicles. For example, these data are used to produce stamping dies for body panels, injection moulds for interior parts, and to order parts from suppliers.
Accuracy and cooperation
Another important task in the model workshop is measuring individual parts and entire cars. They have a specialized centre with top-tier equipment for this. Minor deviations from the required values can often be corrected before the parts are painted. "First, we paint the parts with primer and sand them down to the required values. We assemble everything, measure it, fine-tune it, and secure it so that the individual parts of the model and the whole fit perfectly. Then, we disassemble the model, paint it, polish the parts, and reassemble the whole thing," describes Jaromír Pavlíček.
A perhaps somewhat unexpected helper for modelers is paper tape, which helps to highlight edges, for example
Among the most complex models is the Enyaq shown in the photos. The car is indistinguishable from a production vehicle, and the model even received the beautiful new metallic colour Olibo Green, which looks stunning on the car.
In general, even though the work in the model workshop might first appear to be a combination of sculpting and assembling plastic car models, precision is key. It is crucial at every step because any deviation in the foundation of the model will be amplified in the final result. This is why around 80 people of various professions work on these top-secret models: programmers, designers, machinists, technologists, and modelers who complete the models, among others. As always, cooperation is essential. And it’s not just within the model workshop; it’s within the entire carmaker, with the workshop serving the company’s needs. This is literally where many pieces of the puzzle come together to create a production car.
The components of the models are made by hand, for example the parts of the headlight are created on a 3D printer and the modellers have to polish, color and completely assemble them, then they are assembled into the model
They might already be preparing your next one here.