Learning How to Breathe Life into a Hybrid Car
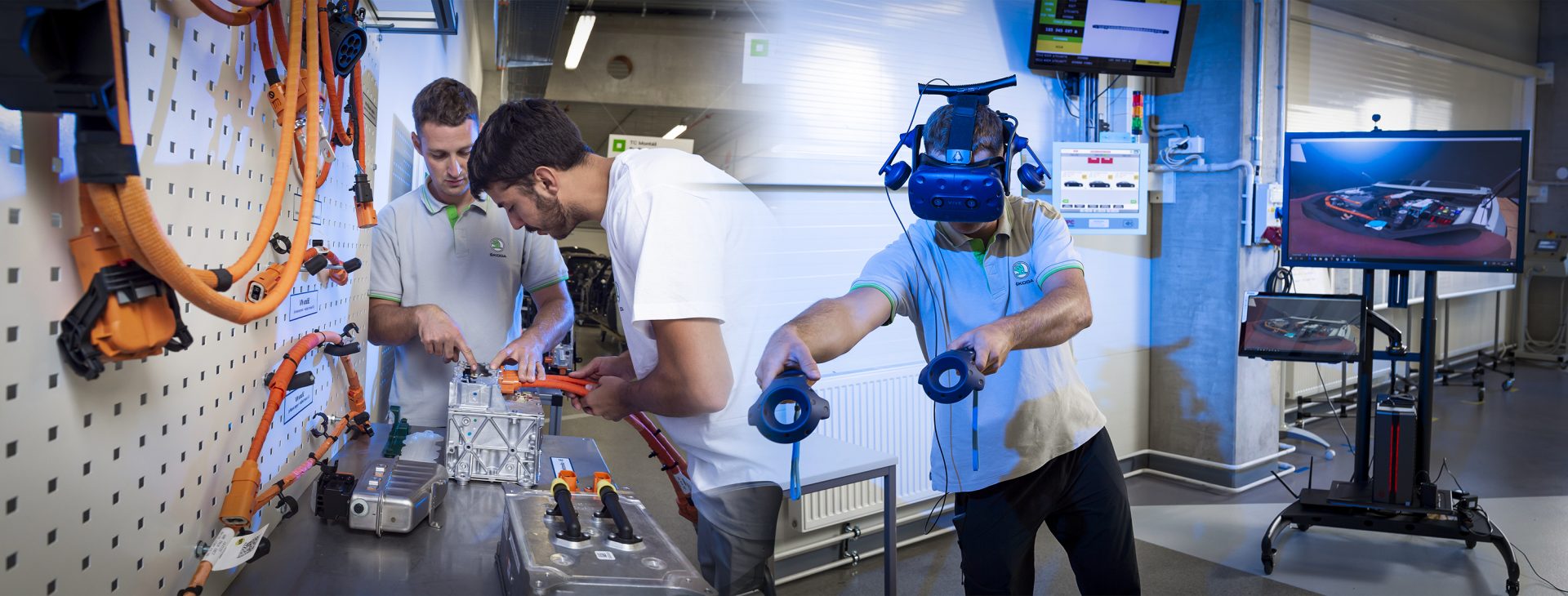
Electromobility is no longer a vision of the future, with ŠKODA starting to manufacture its first electrified production cars. Let’s take a look inside the training centre at the Kvasiny factory in east Bohemia, where the plug-in hybrid ŠKODA SUPERB iV is rolling off the assembly line.
18. 9. 2019 eMobilityMedia Box
10 images
Show more
Show less