Between Carbon and Sulphur
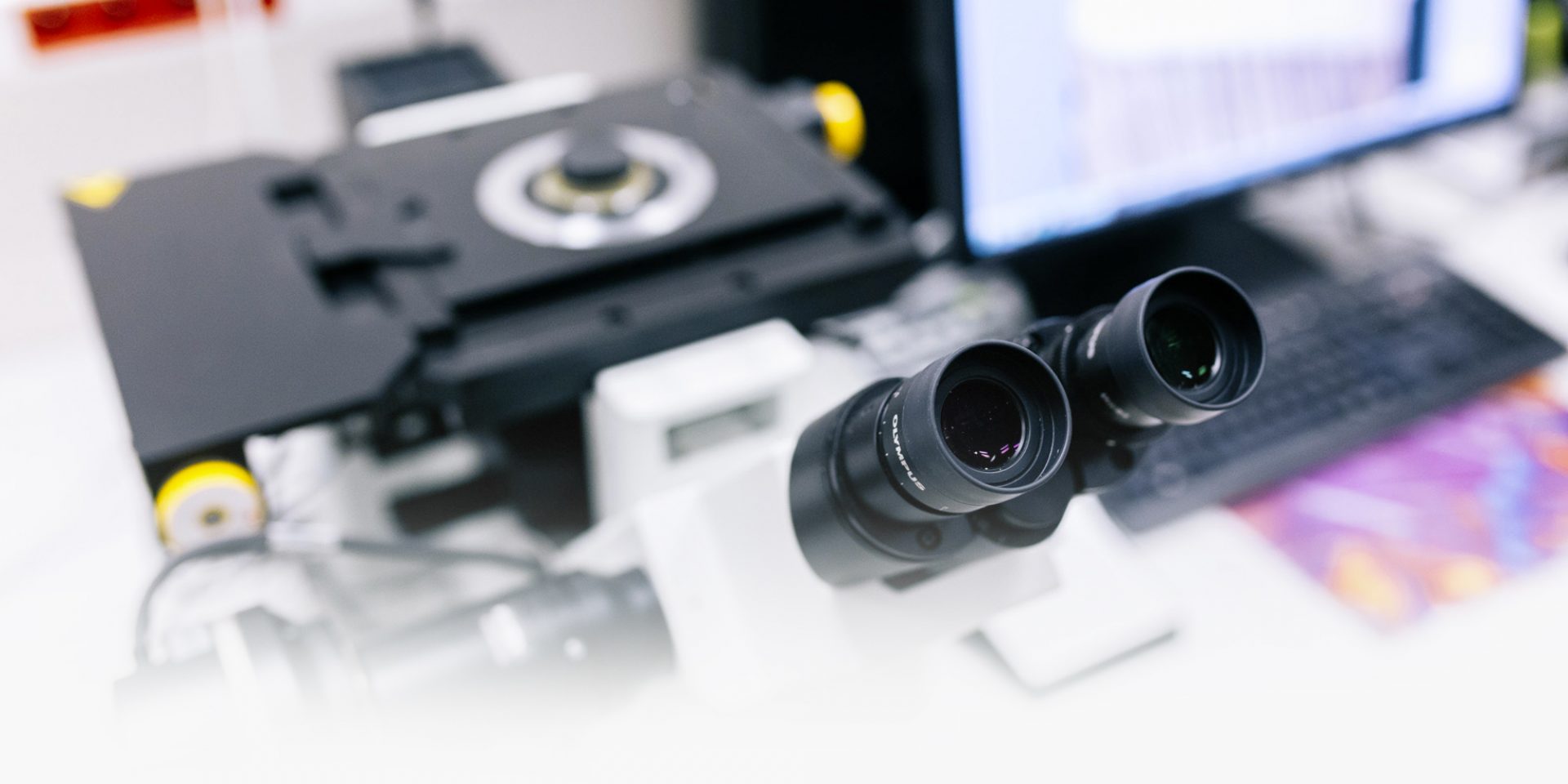
Take a look into the metallic materials laboratory in Vrchlabí where experts test manufactured components every day. The tests they perform are important in approving components for serial production. See the instruments they use in this laboratory – in addition to microscopes, they also have, for example, a saw.
2. 1. 2018 Škoda World Innovation & technologyMedia Box
7 images
Show more
Show less