Step by Step through ŠKODA’s State-of-the-art Paint Shop
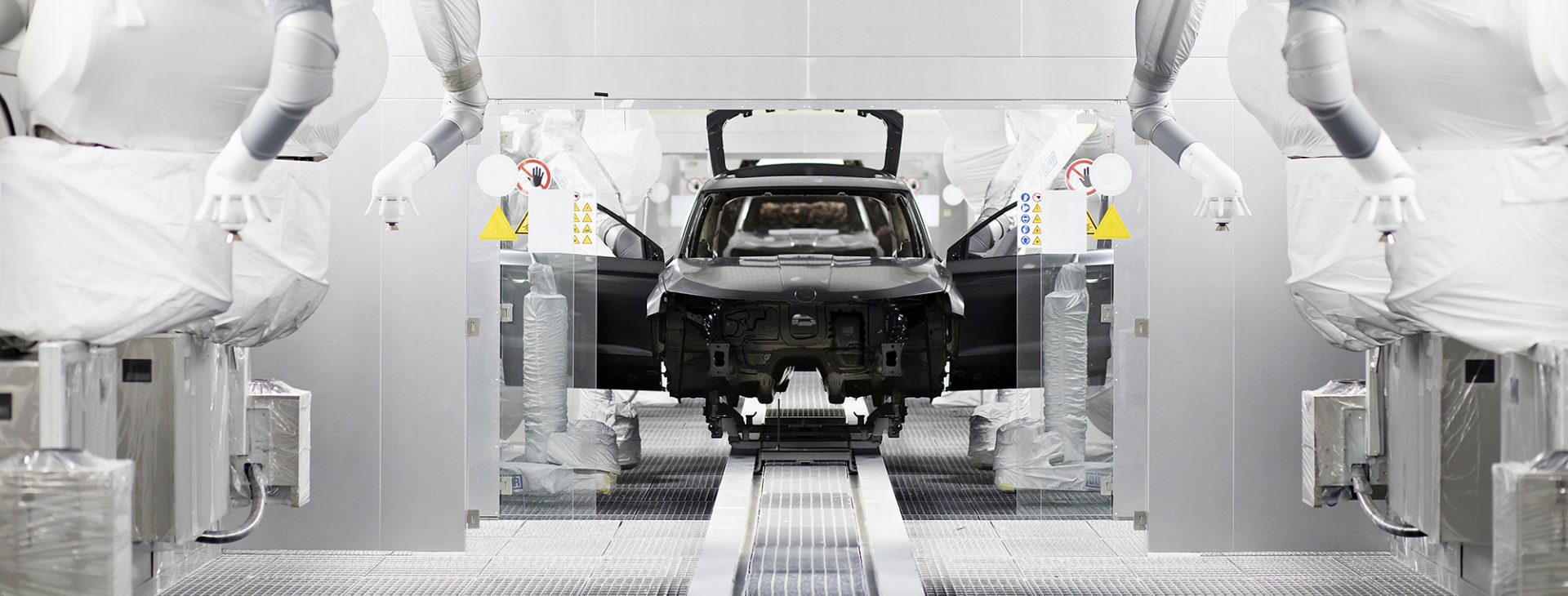
Check out the new paint shop at ŠKODA’s main plant in Mladá Boleslav. Take our step-by-step tour to see how welded bodywork is turned into the precision-painted basis of a new car. Have you any idea what baths, ovens and ostrich feathers are for in a paint shop?
22. 8. 2019 Škoda World Innovation & technologyMedia Box
19 images
Show more
Show less