Quality Time
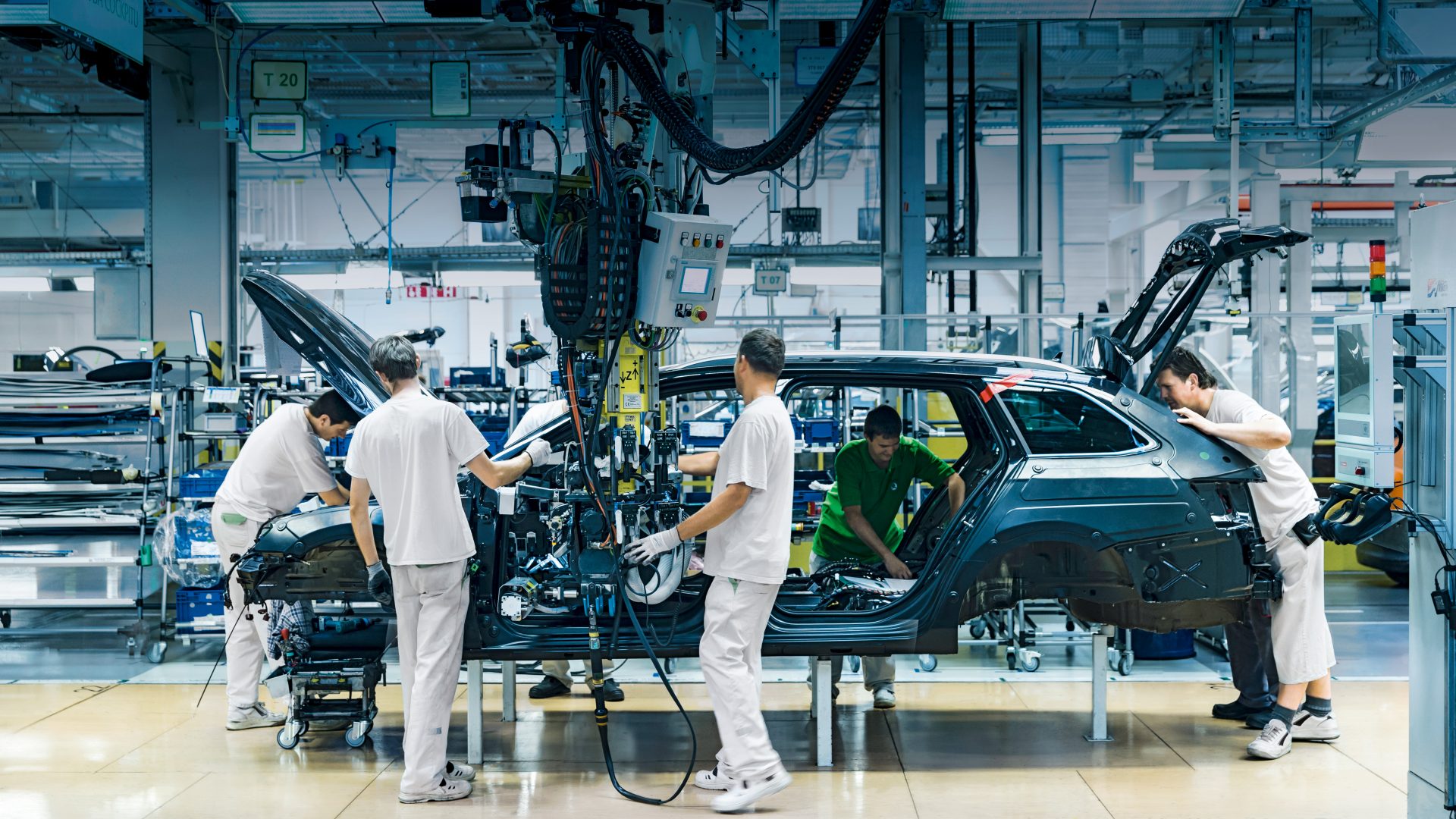
Everything in sync: if you want to feel the drive behind a brand, you’ve got to see where the cars are made. A visit to the ŠKODA plant in Kvasiny, where every ŠKODA Superb makes its first outing.
15. 3. 2016 Škoda World Innovation & technology TechnologyStatus point eight. This marks the end of the very first trip in the life of a Superb, after which it will start driving in earnest. It is the point in production where everything has to be in place. The point where “Čzech it out” is applied literally. Under the merciless glare of special fluorescent lights, more unforgiving than those of any changing room, anything that could be the tiniest of flaws is brought to light. But there are no flaws. The car, which barely 24 hours ago was just individual parts, is now completely finished. And it shines. To experience the first day in the life of a new Superb is to sense the heart of the brand – and to feel the pace of the
assembly process at the production plant in Kvasiny. Not only has the appearance of the car changed, but also its home; large parts of the plant have acquired some major new elements.
Čzech it out
IN THE ORLICKÉ MOUNTAINS
Cars have been made in Kvasiny, a town about 160 kilometres from Prague and on the edge of the Orlické Mountains, for more than 80 years. The mountains are part of the range that forms the border with Poland. Velká Deštná, the highest peak, stands 1,115 metres tall. Rich in castles, fortresses and forests, the area is known for sustainable tourism. It is an ideal place for hikers, and in winter for cross-country skiers.
Information:
www.eaglemountains.cz
THE NEW SUPERB HAS CHANGED EVERYTHING. IT’S LIKE AN AWAKENING FOR US.
TOMÁŠ ŠÍPEK, PRODUCTION EXPERT
ŠKODA’s success and growth are reflected in the development plan for the plant on the gentle foothills of the Orlické Mountains, also known as the ‘eagle mountains’ – and the town’s coat of arms features that proud master of the skies. Historical records mention the place for the first time in 1544, and its castle was the main attraction until the arrival of the carmaker. Kvasiny currently has a population of around 1,500, although the ŠKODA plant employs more than four times that number. Cars have been built here for over 80 years, originally under the brand name of Jawa, while the first Superb type saw the light of day in 1947. The site has produced over 1.5 million cars in total, and now occupies ten times the area enclosed by the original factory walls. The milestones in this expansion process are marked by the Superb model series (see info box).
“Kvasiny is a plant that lives,” says Robert Pek, who has experienced the changes that have occurred since the turn of the millennium first-hand. As an interpreter, he accompanied the new plant director back then during construction. Today he describes the atmosphere like this, “We are living the new age of ŠKODA here. And our family of employees is getting bigger all the time.” While a lot has changed in terms of appearance, the inner values have remained the same. The site has a tradition of manual work in the production of cars, although electric hands are now taking over some of the dirty and heavy work. There are many areas in the plant where one can find such logical and symbolic helping hands between the past and the future.
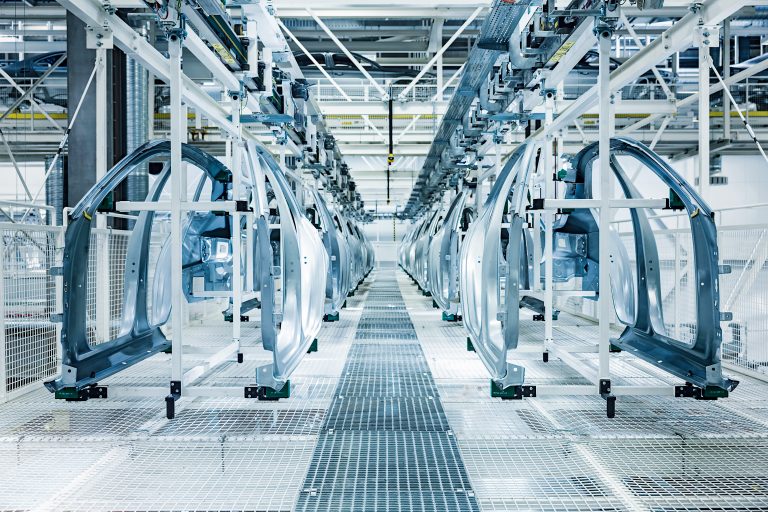
WE ARE LIVING THE NEW AGE OF ŠKODA AT THE KVASINY PLANT.
ROBERT PEK, INTERPRETER
The part of the future that paint specialist Karel Macháček is currently working on goes by the name of Samoa and is a very special hue of metallic red. “As far as technology goes, it’s a complicated application,” says Macháček, “but we like these types of challenges.” A new paint colour called Business Grey came along with the new Superb. Pavel Mizera, who bears overall responsibility for the paint process, knows that a wealth of experience goes hand in hand with high quality. On the new Superb, even the fuel caps are painted in Kvasiny. They were the last blank spot on the paint map. Mizera gazes out over a row of car bodies in gleaming matte gold that glide into an application cage for a special stage of their treatment. There, a descending spray of mist will wash away the last specks of dust, after which the car bodies – already recognisable as Superbs – will be gently stroked with brushes made of emu feathers in order to prevent the build-up of electrostatic charge. The doors are opened by employees in white coats, who call what they do an “operation”. After all, why shouldn’t wellness treatments also extend to cars?
TECHNICAL CHALLENGES? WE LIKE THEM HERE.
KAREL MACHÁČEK, PAINT SPECIALIST
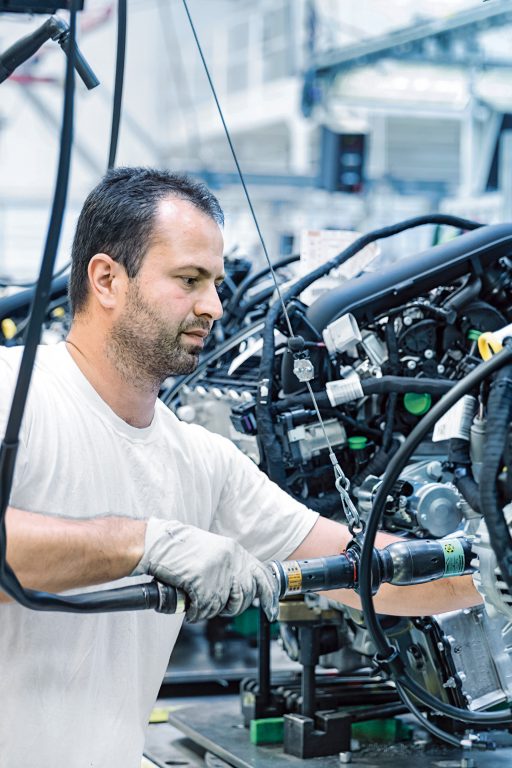
PRODUCTION IS ALL ABOUT SPEED, QUALITY, PRECISION AND RELIABILITY.
PETR BARTÁK, OPERATOR
Including all the priming and drying stages, the conveyor lines in the paint shop cover more than seven kilometres. Those in body production are shorter. That said, the new production hall is enormous. Measuring just over 100,000 square metres, like a huge construction kit. On the Superb’s first outing in its automotive life, it is lifted, pushed, trimmed and caressed. But its genes first need a robust foundation – so the wheel well, front end and longitudinal beams are welded to its underbody. Visitors are immediately struck by how quiet and orderly it is in this enormous hall. The production lines have been restructured and expanded. It is very easy to follow the creation process of the Superb. In the middle of the body shop, robots act out fascinating choreography as they enclose, lift, turn and work on the Superb. From the left and right sides of the hall, workers manually feed preassembled components into the core line’s automated processes. At any given time, 58 cars are on the line, with “assembly” signs at individual stations. Considering production as a holistic process, it is more an awakening. The new Superb required the introduction of new equipment and tools, and a new logistics hall has been built. The body, whose silhouette now clearly reveals it to be the Superb, takes an undulating course through the hall, often suspended just below the high ceiling. There’s no question that the people in Kvasiny have the energy required.
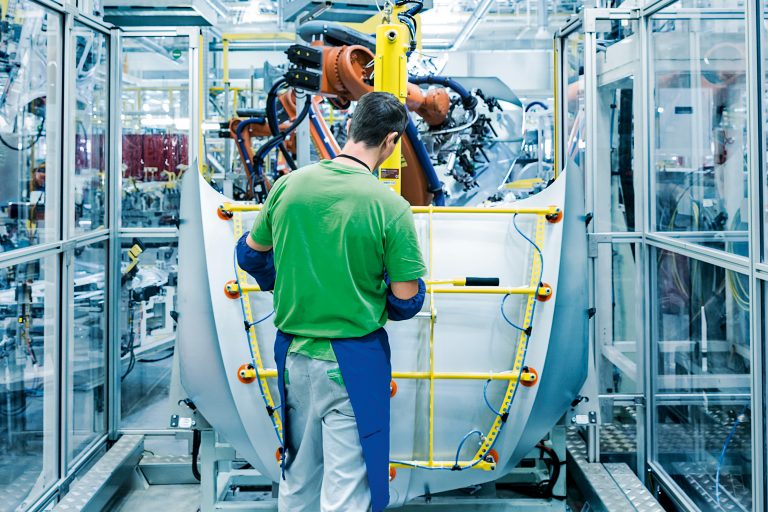
ŠKODA’s most recent production line was built in just one year. “That was like an awakening,” says production expert Tomáš Šípek with pride. “The new Superb has changed everything. The factory is now more generous, brighter, higher and wider – it’s ideal.” For both the Superb and the people who make it. The finishing work on the body before it goes to the paint shop consists of yet another process that sounds simple but is actually rather complicated. Doors, bonnets and hinges are alternately adjusted from back to front. A camera is used to ensure precision when placing the tailgate into a position that the human eye can no longer discern. Tolerance levels here are just about zero, already ensured by in-house quality control that performs random ultrasound measurements during the ongoing production process.
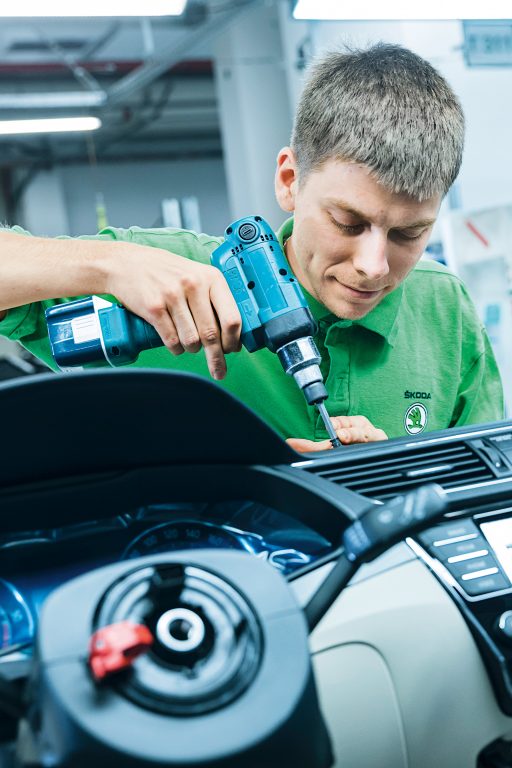
IT’S FASCINATING TO SEE HOW BRAND-NEW TECHNOLOGIES CHANGE OUR DAILY ROUTINES.
MARTIN PRAŽÁK, DASHBOARD ASSEMBLY
One Superb per shift is completely removed from the assembly process and examined at a measurement and test centre designed specifically for this purpose. The room reserved for this fitness check has special security features. All the data needed for the constantly changing and improving automotive production processes of the future are gathered here. Insights that have a direct effect on adjacent linka, as the production line is called. One of the key moments in the life of a Superb is akin to a pit stop in Formula One. Speed and precision are crucial. This is the step that production specialists call the “marriage”, which joins the two main components of body and engine together. The body is elevated to approximately 1.80 metres in order to install the powertrain preassembled by Petr Barták and other operators. The Superb loses its single status in just two minutes of assembly – a shotgun wedding. And the process continues at roughly the same pace. The line weaves through the hall, but the principle remains the same. The components needed for installation are preassembled on the sides of the hall before being fed onto the line. Barcodes ensure that the correct dashboard will be assembled at the station operated by Martin Pražák. And the process keeps on going like a string of beads. Wiring harnesses are laid under the carpet, window regulators and windshield wipers are mounted, and the correct software is installed. The parts are brought in alternately by workers and by self-driving electric transporters. The latter announce their arrival with music – heavy metal, of course!
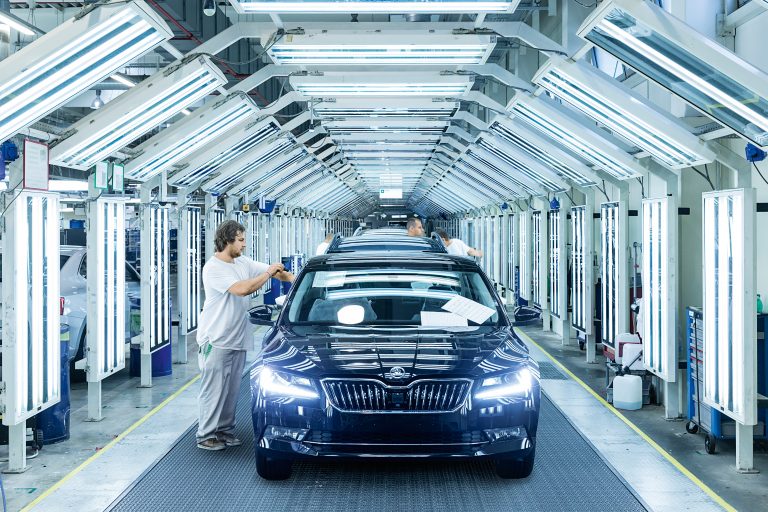
From here on, it gets really serious. This is the territory of strict inspectors such as Petr Förster. This is where the engine is started up for the first time. It is running! But does the car actually move? The first test drive is always a sublime moment. The car makes its way a short distance across the hall, then outside onto a warm-up course right next to the production halls, which includes an asphalt hill. No ŠKODA leaves Kvasiny without first having passed this functional test. The Superb now has all of the necessary genes. Its automotive life can begin. So too can the real driving fun.
EVERYTHING IN KVASINY IS UNDERGOING FURTHER DEVELOPMENT, NOT JUST PRODUCTION.
PETR FŐRSTER, INSPECTOR
Tradition of craftsmanship
Kvasiny also stands for Czech expertise
Car production started in Kvasiny back in 1934, when the Jawa was made. Automotive engineering is therefore anchored in the region, and is constantly being expanded. Today the site is a pillar of the ŠKODA production network, with some 180,000 cars manufactured here every year. Production was restarted in 1947, this time with the Superb. The first modern Superb rolled off the line in 2001, following a complete restructuring of the plant. The production facilities are
to continue undergoing expansion, with some €263 million to be invested by 2018.
Photo: Andreas Pohlmann, Video: ŠKODA AUTO a.s.