PROIZVODNJA BATERIJA: KAKO SE PROIZVODI SRCE ELEKTRIČNOG AUTOMOBILA
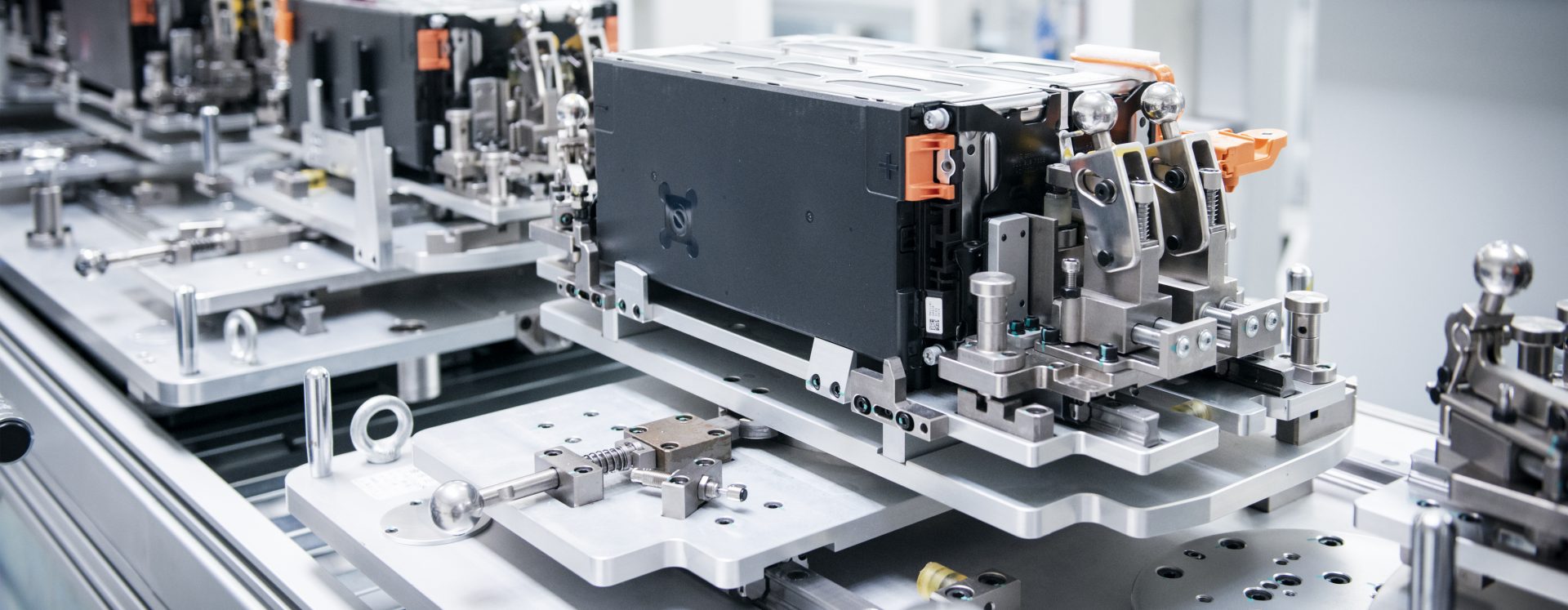
Pogledajte kako se izrađuju baterije za ŠKODA plug-in hibride. Zašto je zaposlenima potrebna posebna radna odeća? Zašto koriste običan flomaster? Zašto mere šrafove?
21. 8. 2020 Škoda svet Inovacija i tehnologija TehnologijaUosvetljenoj, prozračnoj i prostranoj fabričkoj hali linija za proizvodnju baterija na prvi pogled izgleda kao prava linija. Ali ima tri grane, a gotove baterije izlaze otprilike u sredini proizvodne linije. Moduli akumulatora se sastavljaju u sklop od po četiri jedinice u prvoj grani. U drugoj grani nalazi se potpuno opremljeno kućište u kojem su smešteni moduli baterija, koja se na kraju postupka zatvara da bi se zaštitila bateriju od spoljašnjih uticaja. Elektronika baterije sastavlja se u trećoj grani.
Šasija SUPERB iV. Modul baterije nalazi se ispod poda automobila u prednjem delu zadnje osovine.
Tri pravca
U osvetljenoj, prozračnoj i prostranoj fabričkoj hali linija za proizvodnju baterija na prvi pogled izgleda kao prava linija. Proizvodna linija ima tri grane, a gotove baterije izlaze otprilike u sredini proizvodne linije. Moduli akumulatora se sastavljaju u sklop od po četiri jedinice u prvoj grani. U drugoj grani nalazi se potpuno opremljeno kućište u kojem su smešteni moduli baterija, a koja se na kraju postupka sklapanja zatvara da bi se zaštitila bateriju od spoljašnjih uticaja. Elektronika baterije sastavlja se u trećoj grani.
Prilikom sklapanja četiri akumulatorska modula, ŠKODA koristi module eksternog dobavljača koji su u svari gotove male baterije. Ovi moduli se nastavljaju duž prvog dela linije u dva paralelna toka: odvojeno za levi i desni deo baterije. Svaki modul dolazi od dobavljača sa otprilike 20% kapaciteta, pa su od samog početka proizvodnog procesa potrebne mere bezbednosti. Prvi korak je postavljanje modula sa posebnom folijom koja provodi toplotu koja pomaže u poboljšanju hlađenja čitavog kompleta baterija. Između modula se ubacuje hladnjak, koji kada se poveže omogućava da tečnost rashladne tečnosti prolazi kroz hladnjak.
Ostali delovi linije obrađuju niskonaponsku elektroniku baterije. Upravljački modul, poznat kao e-kutija, sa sopstvenom upravljačkom jedinicom, napravljen je na delu linije sa pojačanom zaštitom od prekomernog napona od statičkog elektriciteta. Zbog toga svi na radnom mestu nose posebnu odeću. “Podovi, odeća i obuća imaju ESD sertifikat i redovno se testiraju kako bi se utvrdilo da li štite od statičkog elektriciteta, a to je veoma važno u celoj proizvodnoj liniji“, objašnjava Otakar Mašek, specijalista za montažu baterija. Pojedinačne komponente na liniji su posebno zaštićene.
Otakar Mašek
Specijalista za montažu baterija
Aluminijumsko kućište
Dok se akumulatorski moduli i elektronske kutije montiraju, u drugom delu linije je pripremljena aluminijumska kutiju koja čini telo baterije. Većinu posla u ovoj fazi obavljaju roboti, ali na nekim stanicama imaju manuelnu podršku u slučaju da robot iz nekog razloga ne može da obavi posao.
Masivno aluminijumsko kućište takođe dolazi od dobavljača. Na liniji se oprema sa svim potrebnim komponentama kao što su razni konektori, zavrtnji, graničnici i navoji, ali i spoljašnji toplotni štit koji prolazi kroz središte kućišta i koji štiti bateriju od toplote iz izduvnih gasova koji prolaze ispod nje.
Sastavljene baterije spremne za detaljno testiranje.
Kada je kućište u potpunosti sastavljeno, na red dolazi možda neočekivani pomoćnik, robot koji koristi usisivač kako bi uklonio sve nečistoće koje bi mogle da stvore probleme tokom rada. Nakon usisavanja, kućište je spremano spajanje sa šasijom i motorom, što obavlja robot. Još jedan robot brine o prilično složenom procesu spajanja prethodno povezanog kućišta i modula zajedno na nosaču.
Jednom kada su kućište i moduli sastavljeni, ugrađuju se druge komponente, kao što je rashladni sistem. Instalacija niskonaponskih kablova je završena i kućište dobija materijal za punjenje i potporu. Primenjuje se jedno pametno rešenje nakon što su pričvršćeni na liniji. “Zavrtnji za pričvršćivanje kućišta nalaze se na specijalnim kolicima sa vagom, kako bi se utvrdilo da li je radnik koristio pravi broj šrafova“, kaže Otakar Mašek.
Na početku montaže baterijski moduli su upareni; kompletni blokovi baterija izrađeni su od višestrukih parova modula baterija.
I druga kontrolna praksa može da se čini neočekivanom, a obavlja nakon što su svi konektori pričvršćeni unutar baterije, tako što zaposleni u sledećoj stanici flomasterom pravi tačku na mestu spajanja kako bi potvrdio da je izvršio drugu vizuelnu proveru konekcije. “Ovaj zahtev primorava zaposlenog da zapravo pogleda vezu“, kaže Mašek. Nakon toga preostaje samo povezivanje modula sa kontrolnom jedinicom i baterija je spremna za zatvaranje. Poklopac na kućištu je pričvršćen dvostrukim zatvaračem, gumom i posebnim lepkom, koju zatvara robot.
Mnogo testova
Montažu prati niz testova. Prvo se ispituje kako je baterija zatvorena, sa odvojenim proverama nepropisnosti rashladnog sistema i baterije u celini. Povremeno se među testiranim baterijama pojavi jedinica drugačijeg izgleda, što potvrđuje da aparat za ispitivanje zatvaranja radi ispravno. Specijalni mlazovi mogu da simuliraju nedostatke zatvarača, što dodaje novu dimenziju proveri funkcionalnosti uređaja za ispitivanje.
Proizvodnja baterija je čista i gotovo bešumna, sa malo ručnog rada. Ručni rad je uglavnom potreban za završne faze montaže.
Kada baterija prođe test zatvaranja može da pređe u jedno od trinaest ispitnih faza u okviru kojih se odvija niz električnih ispitivanja. Proveravaju se visokonaponski i niskonaponski (komunikacioni) delovi i sprovode se ispitivanja kako bi se osiguralo da izolacija pravilno funkcioniše. Kada prođe kroz sva ispitivanja, baterija se puni do oko 37% kapaciteta. Zatim se dodaje nalepnica sa upozorenjem, etiketa za identifikaciju (ova nalepnica se takođe štampa i postavlja automatski pod budnim okom kamere) i nekoliko drugih detalja. Zatim se gotova baterija šalje u skladište.
Linija za proizvodnju litijum-jonskih baterija za plug-in hibride
• Dnevni kapacitet: 720 jedinica
• Godišnji kapacitet: 180.000 jedinica
• Vreme ciklusa: 88 sekundi
• Trajanje montaže: približno 2 sata
• Broj stanica: 66
• Linijsko osoblje: 58
• Proizvodna površina: 2,000 m2
• Investicije: EUR 25.3 miliona
Skladište gotovih baterija. Stalno ga nadgledaju termalne kamere koje otkrivaju svaki rizik od požara.